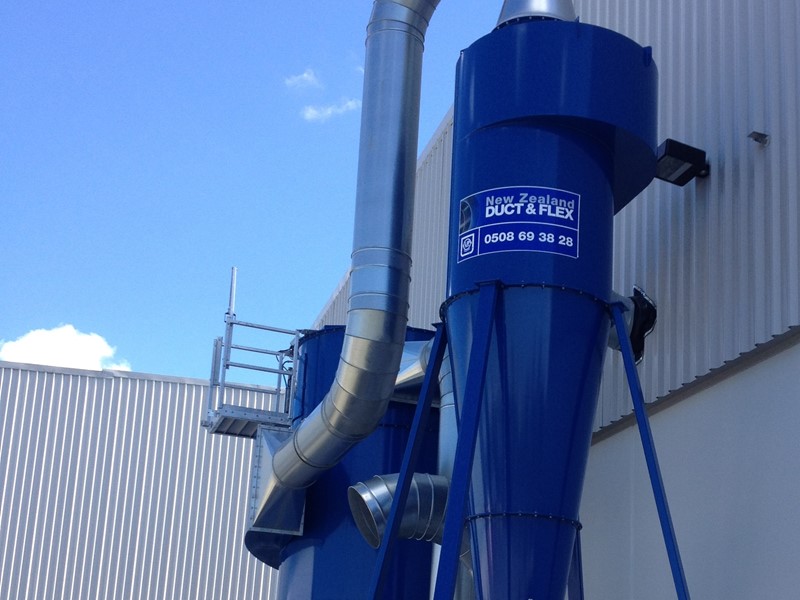
Local tyre retreader invests in Clean, Green New Zealand
In New Zealand Bridgestone operate 4 re-tread sites managed by National Engineering Manager Vaughan Childs. “The company policy worldwide is Serving Society with Superior Quality.” says Vaughan “This is included on all aspects of our business: not only the quality of the product we produce but also the way we produce it, the effect on our atmosphere, neighbours and (most importantly) our staff.”
‘Nil’ emissions target
Three years ago Bridgestone began an investment in ‘Nil Emissions’ worldwide and as a part of this, the sites around New Zealand started to be upgraded - beginning with Bridgestone Rotorua.
Generally the plant collected the dust and fumes via a cyclone with the bulk of the dust deposited into bags at the base ready for recycling. However, staff sometimes noticed small amounts of dust escaping from the top of the cyclone. “Clearly we could improve this process,“ confirmed Vaughan Childs.
Getting a bigger cyclone was the first choice but further investigation found that even the best cyclones in the world only capture around 80% of the fine dust that enters them, and it’s this very light fine dust that adds to smog, dust nuisance, poor air quality and contributes to human respiratory problems.
Bridgestone contacted a number of companies and settled on local company New Zealand Duct & Flex to design and install a Danish-manufactured world quality system to produce the lowest impact possible on the staff and neighbours’ environment.
Just 12 weeks later a crane was lifting the new unit into a very restricted space on a Friday to reduce restrictions to production. Vaughan says “The effect was immediate: suction greatly improved, staff found factory air quality noticeably better and we also found, due to the efficiency of the new extraction system, we were filling rubber shaving collecting crates so fast we had to buy more crates, and the recycling company bought a bigger truck to take them!”
Vaughan Childs from Bridgestone summarised the whole install saying “Geoff and JKF Industri with the assistance of local NZ suppliers and contractors provided us ultimately with world class performance in Rotorua, hence the next site – Auckland, was awarded to New Zealand Duct & Flex as well”.
Success leads to second site install
The Auckland site involved a totally new factory projected to ultimately operate at a much higher level than Rotorua. The extra capacity would not be required immediately so a system was planned that would not waste energy in the early days, but at no extra cost allow Bridgestone to increase up to 50% in a year or two.
The recommended installation was a JKF unit with PowerPlus® allied to a JKF pre-separator cyclone that acts as the feed for the recycled rubber being collected in the bags. PowerPlus® is the very latest JKF Filter design with world leading energy conservation features:
- Cleaning- PowerPlus® controls the filter automatically, monitoring differential pressure, only initiating a cleaning cycle if it detects the filter bags need cleaning. This obviously saves large amounts of compressed air as the usual units just pulse air every 30 seconds or so, also reducing wear and tear on the filter bags.
- Pulse Control-PowerPlus® also controls the force of the cleaning by monitoring the filter performance and so adjusts automatically the total amount and even the ‘force’ of the pulse between 2 and 5 bar. More compressed air is saved with reduction in wear of the bags
- Single bag cleaning- PowerPulse® cleans each bag individually giving precise accurate and consistent cleaning to the whole filter bag system
PowerPlus® has been shown to save between 25-50% of the compressed air used by other systems. Bridgestone Auckland started production in November operating at 50-60% capacity. So far due to the efficiency of the system and PowerPlus® cleaning, the savings have been in excess of 90% of compressed air against a normal manually set filter cleaning system. The fan is also controlled by a variable speed drive, again saving energy but allowing Bridgestone, if new machinery is added, to increase suction immediately. The filter needs no intervention: it will adjust to suit the dust load by itself.
Vertical Force Ventilation
The JKF units include a VFV safety system. This simply means, in the unlikely event of an explosion in the dust filter, the unit releases any explosion harmlessly up to the sky rather than sideways where it might cause damage to equipment, the building and staff.
The force of the explosion is released, no fire escapes to atmosphere and no damage occurs to the filter. Refitted with new filter socks and explosion release membranes the filter can be operating again on the same day.
Vaughan Childs summarised “All the features of this unit are attractive - its safety, long-term running costs, the energy and environmental considerations. When your company is a household name, it’s important not only to talk about the environment but action those ideals. With the media and personal communications being so much a part of everyday life, it is vital all our actions withstand outside scrutiny. We are very fortunate to live in maybe the most unspoilt country in the world; the team at Bridgestone NZ are doing our best to help keep it that way.”