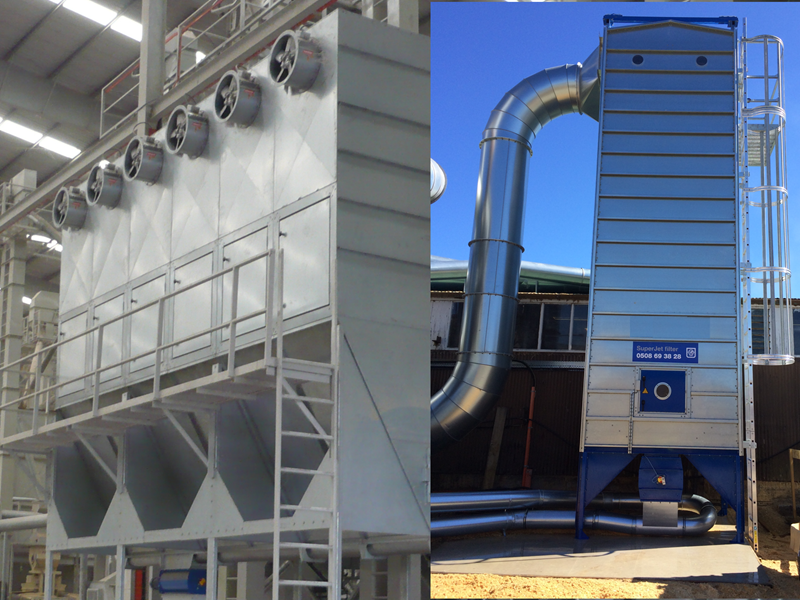
How do dust extraction filters get cleaned?
As wood and processing industries grew their demand for ever larger dust extraction filters, the dust collectors grew to a point where they could not fit the space available. In order to overcome this, manufacturers fitted various cleaning systems to help dislodge the dust from the filter socks or cartridges in their dust extraction solutions.
Vibration Cleaning
A basic vibrating method: a simple electric motor that occasionally shakes a frame from which the filter socks are hung. This shaking helps release dust in the same way hitting the outside with a stick does!
Advantages
Cheap and simple, they are often known as Shaker systems for dust extraction solutions
Disadvantages
Generally it is better to spend the money on good quality ANTI-STATIC socks – these filters are more unreliable and can need more maintenance for this mechanism to work.
Reverse or Regenerating fans
Larger dust extraction filter units are divided up into compartments, and then fans are fitted to the exits.
Normally operated on timers, these fans come on one at a time and blow air back through the filter compartment they are fitted to. This has the effect of blowing air back through the filter socks, to help dislodge the dust.
Advantages
- gentle on the bags and no need for compressed air
Disadvantages
- Added cost : Powerful 2.2kw fans are needed with associated wiring and electrical systems
- Additional power: Running these 2.2kw fans needs additional power
- You really need a minimum of 3 compartments in the dust collector as this reverse airflow effectively takes out that compartment for a period so overall suction in the factory area reduces
- When fitted in 2 compartment filters, all this air and the air from the main extraction fan has to escape from the one filter chamber affecting efficiency. The reverse fan may struggle to produce enough power to clean and / or give voltage trip problems
- They are particularly efficient when the main fan is switched off as they are not fighting the power of the larger extraction fan. Each compartment can be pulsed one at a time – the air escaping out of the other compartments but once the main fan is off, unless you have a method to stop the dust being blown back down the main duct into the factory, fine dust makes its way back inside coating everything in dust again
- These fan systems normally come with a control unit from the supplier or separate electrical contractor. This cost combined with the cost of an automated valve to close the main duct off can be as much as the dust extraction filter unit itself
- Overseas electrical systems may, or may not, meet your electrical contractor’s safety concerns…especially if they didn’t get the work to make the control unit themselves
- There is more to go wrong generally – if you can allow the extra space to have a basic bag house dust extraction solution with no cleaning, this may be an option to consider
Compressed Air Cleaning
These systems in dust collectors are the most efficient in terms of dust removal in any dust extraction system. Compressed air is blown in short pulses into the end of the filter bag (or cartridge) blowing the dust off. These pulses are very short – less than a second - so the ‘blow back ‘into the factory is limited – and nothing if the main fans running. If there are a number of filters, then the overall effect on the suction is very small and hence not a problem.
Advantages
- Very Efficient, short pulse doesn’t affect overall system extraction noticeably
- A small relatively smaller filter unit can deal with a relatively large dust and air flow
Disadvantages
- Cost : Compressed air needs compressors which can be expensive to buy and run
- Correct maintenance: Systems need correct design and attention so that water doesn’t enter the system and get pulsed at high pressure into filter cartridges – which can destroy them
- Maintenance costs : Compressed air pulses are hard on the filter material causing damage and replacement times are lower that say reverse fans
- Staff knowledge required : For non technical staff there is more to service / maintain
- Manufacturer support : Normally needs manufacturer’s agents or similar to service periodically to prevent breakdowns / expensive filter replacements